Последнее обновление: 03.04.2025
Законодательная база Российской Федерации
8 (800) 350-23-61
Бесплатная горячая линия юридической помощи

- Главная
- "НОРМЫ РАСЧЕТА НА ПРОЧНОСТЬ СТАЦИОНАРНЫХ КОТЛОВ И ТРУБОПРОВОДОВ ПАРА И ГОРЯЧЕЙ ВОДЫ. РД 10-249-98" (утв. Постановлением Госгортехнадзора РФ от 25.08.1998 N 50) (раздел 8) (ред. от 13.07.2001)
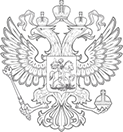
"НОРМЫ РАСЧЕТА НА ПРОЧНОСТЬ СТАЦИОНАРНЫХ КОТЛОВ И ТРУБОПРОВОДОВ ПАРА И ГОРЯЧЕЙ ВОДЫ. РД 10-249-98" (утв. Постановлением Госгортехнадзора РФ от 25.08.1998 N 50) (раздел 8) (ред. от 13.07.2001)
(в ред. Изменения N 1, утв. Постановлением Госгортехнадзора России от 13.07.2001 N 31)
Дата введения 2001-09-01
: Разделы 1 - 3 Норм расчета на прочность стационарных котлов и трубопроводов пара и горячей воды. РД 10-249-98 включен в базу отдельным документом.
Раздел 4 Норм расчета на прочность стационарных котлов и трубопроводов пара и горячей воды. РД 10-249-98 включен в базу отдельным документом.
Раздел 5 Норм расчета на прочность стационарных котлов и трубопроводов пара и горячей воды. РД 10-249-98 включен в базу отдельным документом.
Разделы 6 - 7 Норм расчета на прочность стационарных котлов и трубопроводов пара и горячей воды. РД 10-249-98 включен в базу отдельным документом.
Раздел 9 Норм расчета на прочность стационарных котлов и трубопроводов пара и горячей воды. РД 10-249-98 включен в базу отдельным документом.
Разделы 10 - 12 Норм расчета на прочность стационарных котлов и трубопроводов пара и горячей воды. РД 10-249-98 включен в базу отдельным документом.
УТВЕРЖДЕНЫ постановлением Госгортехнадзора России от 25.08.1998 N 50
Редакционная коллегия: В.С.Котельников, Н.А.Хапонен, А.А.Шельпяков (Госгортехнадзор России)
Ю.К.Петреня, Е.Э.Гильде, А.В.Судаков, А.А.Чижик, И.А.Данюшевский, П.В.Белов, А.М.Рейнов (АООТ НПО ЦКТИ им. И.И.Ползунова)
8. РАСЧЕТ НА ПРОЧНОСТЬ ФЛАНЦЕВ ТЕПЛООБМЕННЫХ АППАРАТОВ И ТРУБОПРОВОДОВ8.1. Условные обозначения8.8.1. В разделе приняты следующие условные обозначения, представленные в табл.8.1.
Таблица 8.1
Обозначения геометрических размеров фланцевых соединений приведены на рис.8.1 и 8.2.
Рис. 8.1. Фланцы с коническим переходом
Рис. 8.2. Плоские фланцы
8.2. Общие положения8.2.1. В Нормах рассматриваются фланцы с коническим переходом (конической втулкой) и плоские фланцы, а также жесткие фланцы и свободные.
8.2.2. Деталями фланцевого соединения являются фланцы, кольцо свободного фланца, прокладка, мембрана, шпильки (болты), гайки, шайбы.
Под элементами фланца понимаются цилиндрическая часть фланца, конический переход, тарелка фланца, бурт свободного фланца, нажимное кольцо, отверстия под шпильки, выступы, впадины и др.
8.2.3. Применение болтов допускается до давления 3,0 МПа и температуры 300 °С, для болтов по ГОСТ 20700 предельная температура допускается до 400 °С.
8.2.4. Требования к конструкции, материалам и полуфабрикатам, а также к изготовлению и контролю качества рассматриваемых фланцев должны соответствовать требованиям соответствующих Правил Госгортехнадзора России (т.е. по котлам, сосудам или трубопроводам ТЭС в зависимости от назначения изделия, к которому привариваются рассматриваемые фланцы).
Дополнительно должны соблюдаться следующие условия:
расположение и конструкция опор на корпусе, днище или трубопроводе должны обеспечивать отсутствие передачи внешних нагрузок на фланцевое соединение, превышающих величину, приведенную в п. 8.7.6.5;
расстояние от конического перехода фланца или тарелки плоского фланца до кромки сварного шва приварки опоры должно быть более величины, рассчитанной по формуле , но не менее 100 мм;
величина предварительного затяга фланцев с приварным мембранным уплотнением не должна превышать 30% расчетного усилия на шпильки при действии внутреннего давления;
величина подгрузки шпилек от разности температур между фланцами и шпильками не должна превышать 30% расчетного усилия на шпильки при действии внутреннего давления.
8.2.5. Нормы содержат методику расчета на прочность фланцев с прокладочным и мембранным уплотнением для обоснования их основных размеров.
В основу расчета на прочность фланцевого соединения заложен метод предельных нагрузок с проверкой напряжений по наиболее напряженным сечениям фланца.
Поверочный расчет на усталость деталей фланцевого соединения должен выполняться для оборудования ТЭС в соответствии с требованиями раздела 5 Норм.
8.2.6. Допускается использование фланцевых соединений без расчета по обоснованию выбора основных размеров при изготовлении их в соответствии с ГОСТ 12815 - ГОСТ 12822.
8.2.7. Фланцевые соединения, рассчитанные по настоящей методике, гарантируют не менее 1000 циклов подъема и сброса давления при сроке службы 100 тыс.ч.
8.3. Расчетное давление8.3.1. Под расчетным давлением фланцевого соединения следует понимать избыточное давление, на которое производится расчет на прочность фланцевого соединения.
8.3.2. Расчетное давление фланцевого соединения следует принимать не менее расчетного давления изделия.
8.3.3. Если давление гидравлического испытания изделия p_h превышает 1,3 расчетного давления изделия, то следует выполнить расчет фланцевого соединения на условия гидравлического испытания. Если p_h < 1,3p, то такой расчет можно не выполнять.
8.4. Расчетная температура8.4.1. Под расчетной температурой металла рассчитываемой детали фланцевого соединения следует понимать температуру, по которой принимается значение допускаемого напряжения.
8.4.2. Расчетную температуру металла фланца следует принимать равной расчетной температуре металла изделия в рабочих условиях. Если выполняется расчет на условия гидравлического испытания согласно п.8.3.3, то в качестве расчетной температуры принимается температура гидравлического испытания.
Расчетную температуру металла фланцевого соединения, необогреваемого горячими газами или надежно изолированного от обогрева извне, следует принимать равной температуре, содержащейся в нем рабочей среды без учета допусков по отклонению температуры от номинального значения, установленных ГОСТ 3619, ГОСТ 21563, ГОСТ 22530.
8.4.3. Если температура металла ниже 80 °С, то за расчетную принимается температура 20 °С.
8.4.4. Расчетную температуру шпилек, в том числе ввертных, следует принимать равной 0,95 от расчетной температуры фланца.
8.4.5. Расчетную температуру металла мембран следует принимать равной расчетной температуре фланца.
8.5. Допускаемые напряжения8.5.1. Допускаемое напряжение металла фланца следует принимать согласно разделу 2 Норм.
Допускаемые напряжения для шпилек, изготовленных из широко используемых для крепежных изделий сталей, следует принимать по табл. 8.2.
Таблица 8.2
Допускаемое напряжение для шпилек из углеродистых и низколегированных сталей, МПа
Для шпилек диаметром менее 24 мм допускаемые напряжения [o_s], принимаемые по табл.8.2, необходимо умножить на величину поправочного коэффициента K_0, принимаемого по табл.8.3 или по формуле
Таблица 8.3
Выбор поправочного коэффициента
Шпильки диаметром менее 24 мм рекомендуется применять с контролируемым затягом.
8.5.2. Допускаемые напряжения для шпилек, изготовленных из марок сталей, не указанных в табл. 8.2, или по которым имеются специальные технические требования и данные по гарантированным характеристикам кратковременной и длительной прочности, следует определять по формуле
где o0,2 / t - минимальное значение условного предела текучести при остаточной деформации 0,2% при расчетной температуре металла шпилек (в том числе при t = 20 °С), МПа;
- среднее значение предела длительной прочности на заданный ресурс (10(5) или 2·x 10(5) ч) при расчетной температуре металла шпилек, МПа.
8.5.3. Допускаемые напряжения металла фланца и шпилек, имеющие номинальный диаметр резьбы, больше номинального диаметра гладкой части, в условиях гидравлического испытания и монтажа принимаются равными
при наличии гарантированных характеристик металла или , где [o_s] и [o_f] принимаются в соответствии с п.8.5.1.
Допускаемые напряжения металла шпилек с одинаковыми номинальными диаметрами резьбы и гладкой части в условиях гидравлического испытания принимаются равными
8.6.1. Номинальные размеры деталей фланцевого соединения и фактические размеры должны быть не менее расчетных.
8.6.2. Если при контроле фактических размеров фланцев обнаруживается отклонение какого-либо расчетного параметра в сторону понижения запаса прочности более чем на 5%, то следует выполнить расчет фланцевого соединения по фактическим размерам.
Фактическое значение шага между отверстиями не должно отличаться от принятого в расчете более чем на 5% в обе стороны.
8.7. Предварительный выбор размеров деталей фланцевого соединения8.7.1. Исходные данные8.7.1.1. Геометрические размеры изделия: толщина стенки s и внутренний диаметр D. Внутренний диаметр фланца следует принимать равным внутреннему диаметру изделия.
8.7.1.2. Расчетное давление фланцевого соединения p.
8.7.1.3. Допускаемые напряжения при расчетной температуре, при 20 °С и при условии гидравлического испытания для металла фланца и шпилек, принимаемые по заданной или выбранной марке стали, обозначаются
8.7.1.4.Толщина стенки цилиндрического участка фланца с коническим переходом s1, а также цилиндрическая часть плоского фланца
s1 = s + s
где s - плюсовое отклонение на толщину стенки. Во всех случаях s1 должно быть не менее 5 мм.
8.7.1.5. Высота цилиндрического участка фланца с коническим переходом h1 должна приниматься равной s1, но не менее 10 мм.
Допускается при s1 >= 20 мм принимать h1 >= 0,8s1 при условии, что уменьшение цилиндрического участка не будет препятствовать контролю сварного соединения фланца с изделием.
8.7.1.6. Диаметры шпилек и отверстий под шпильки принимаются по табл. 8.4. Таблица составлена на основе применения шпилек с крупным шагом по ГОСТ 24705. При использовании других резьб следует внести соответствующие изменения в табл. 8.4.
Таблица 8.4
Размеры шпилек, рекомендуемые для фланцевых соединений
8.7.1.7. Рекомендуемые значения диаметров шпилек в зависимости от условного давления p_y и условного диаметра D_y приведены в табл. 8.5.
Таблица 8.5
Рекомендуемые диаметры шпилек
При выполнении расчетов на ПЭВМ рекомендуется выбор диаметра шпилек начать с меньшего значения d_0s.
8.7.1.8. Тип, конструкция, материал и основные размеры прокладок, а также их характеристики принимаются по табл. 8.6, 8.7, 8.8 в соответствии с типом и конструкцией фланца.
Таблица 8.6
Значение пределов текучести o_0,2 для металлов плоских, профильных и зубчатых прокладок
Размеры прокладок
Эффективная ширина прокладок, удельное давление на прокладку и коэффициент m
Примечание. Напряжение o_0,2 принимается при температуре 20 °С; K1 = 0,8.
8.7.2. Определение размеров прокладки8.7.2.1. Расстояние от внутренней кромки фланца до внутреннего диаметра прокладки u принимается по табл.8.9.
Таблица 8.9
Примечание. - толщина прокладки, высота зубца, диаметр прутка или наибольшая высота профильной прокладки, мм.
8.7.2.2. Наружный диаметр прокладки определяется по формуле
D_d = D + 2b_0 + 2u.
Для профильных прокладок b_0 - ширина профиля (наибольший размер).
Для плоских приварных фланцевых соединений
D_d = D + 2s1 + 2b_0 + 2u.
8.7.3. Выбор размеров конического перехода8.7.3.1. Относительная толщина конического перехода у основания фланцевого соединения K предварительно принимается согласно табл. 8.10.
8.7.3.2. Толщина конического перехода определяется по формуле s2 = Ks1.
При выполнении расчетов на ПЭВМ рекомендуется первоначально принимать s2 = 2s1.
8.7.3.3. Высота конического перехода предварительно принимается равной h2 = 3s1
8.7.4. Геометрия размещения шпилек и выбор наружного диаметра фланца8.7.4.1. Диаметр окружности шпилек и наружный диаметр фланца определяются по формулам:
с для фланцев с коническим переходом
для плоского фланца
для плоского приварного фланца
для опорного бурта
D_f = Ds - d_0 - (2 + 8),
где геометрические размеры a, a1, e, d_0 (см. рис. 8.1) принимаются в зависимости от выбранного наружного диаметра шпильки (см. табл.8.4). Геометрический размер a принимается не менее радиуса перехода r от шейки фланца или от цилиндрического участка фланца к тарелке фланца.
Радиус перехода r рекомендуется принимать в пределах (0,6 - 0,8)s, но не менее 6 мм при D =< 600 мм; 10 мм при 600 < D < 1000 мм; 12 мм при D >= 1000 мм.
Примечание. Допускается уменьшение диаметра окружности шпилек и наружного диаметра фланца при условии обеспечения возможности сборки и затяга шпилек.
8.7.4.2. Значение шага шпилек должно находиться в пределах, указанных в табл. 8.11, и выбирается исходя из опыта эксплуатации аналогичных фланцевых соединений.
Таблица 8.11
Рекомендуемое значение шага шпилек из условия местного раскрытия фланцевого соединения принимается:
при pD =< 1200 | l`s = 45d_0s (pD)(-0,43); |
при pD > 1200 | l`s = 2,1d_0s - для обычных гаек; |
l`s = 1,5d_0s - для колпачковых гаек. |
Принимается значение числа шпилек z, округленное в большую сторону. Рекомендуется принимать число шпилек кратным четырем.
Допускается при z` > 8 принимать значения числа шпилек, округленные до ближайшего большего целого числа, при z` < 8 число шпилек должно быть кратно двум, но не менее четырех шпилек.
8.7.4.4. Уточненное значение шага шпилек
8.7.4.5. Расчетный диаметр прокладки определяется по формуле
Dm = D_d - D_0
8.7.4.6. Наружный диаметр мембраны определяется по формуле
8.7.5. Определение усилий на шпильки8.7.5.1. Минимальное усилие, необходимое для обжатия прокладки
где b, b_0, q_0 принимаются согласно п. 8.7.1.8.
При уплотнении мембранного типа Fd = 0.
8.7.5.2. Минимальное усилие на прокладку, необходимое для сохранения плотности при рабочем давлении и давлении гидравлического испытания
где q = mxp - удельное давление на прокладку в рабочих условиях МПа;
q_h - удельное давление на прокладку при гидравлическом испытании, МПа;
q_h = 0,8mxp_h,
здесь произведение mx выбирается по табл.8.12.
Таблица 8.12
Прокладка | mx | |
Фланцы сосудов | Фланцы трубопроводов | |
Плоская, комбинированная | 1,2 | 1,5 |
Профильная, зубчатая | 1,5 | 2,0 |
Для металлических прокладок коэффициент x принимается равным единице. Для остальных прокладок коэффициент x выбирается по табл. 8.13.
Таблица 8.13
При уплотнении мембранного типа F2 = 0, F_2h = 0.
8.7.5.3. Растягивающие усилия в шпильках от рабочего давления и давления гидравлического испытания определяются по формулам:
при уплотнении прокладочного типа
при уплотнении мембранного типа
8.7.5.4. Расчетные усилия, воспринимаемые шпильками, следующие:
при уплотнении прокладочного типа
F_0 = max{Fd, Ft} - усилие затяга,
F_oh = F_2h + F_h - усилие при гидравлическом испытании,
F_0 = F2 + Fp - усилие в рабочих условиях при расчетной температуре ниже 400 °С,
Ft = max{F2 + (1,0 + n) Fp, Fd - 0,5(n - 0,2) Fp} - усилия в рабочих условиях при расчетной температуре, равной или более 400 °С;
при уплотнении мембранного типа
F_0 = 0,3Fp - усилие затяга во фланцевом соединении, работающем при расчетной температуре ниже 400 °С,
F_0 = (0,3 + 0,5n) Fp - усилие затяга во фланцевом соединении, работающем при расчетной температуре, равной или более 400 °С,
F_0h = F_h - усилие при гидравлическом испытании,
Ft = 1,3Fp - усилие в рабочих условиях.
Коэффициент n, учитывающий влияние ползучести, следует принимать по табл.8.14.
Допускается принимать меньшее значение коэффициента n, если это обосновано расчетом релаксации напряжений в шпильках и резьбе.
8.7.6. Проверка условий прочности в шпильках8.7.6.1. Напряжение растяжения в шпильках при затяге определяется по формуле
.
8.7.6.2. Напряжение растяжения в шпильках при гидравлическом испытании определяется по формуле
.
8.7.6.3. Напряжение в шпильках в рабочих условиях определяется по формуле
.
8.7.6.4. При невыполнении одного из условий прочности расчет следует повторить с п.8.7.4.3, последовательно увеличивая число шпилек z на величину z + 4 и проверяя условия по пп.8.7.6.1-8.7.6.3. Окончательное число шпилек z не должно превышать значение
z = zKэ,
где Kэ - коэффициент, определенный экономическим расчетом для конкретных условий производства. При отсутствии такого расчета Kэ =1,07-1,12. Если при числе шпилек z = zKэ условия прочности не выполняются, то расчет повторить с п. 8.7.1.6, приняв большее значение диаметра шпилек.
8.7.6.5. Изгибающий момент от внешних нагрузок допускается без дополнительных расчетов, если его значение удовлетворяет условию:
.
8.7.7.1. Предварительно толщина тарелки фланца выбирается исходя из опыта эксплуатации аналогичных фланцевых соединений.
8.7.7.2. Для оценки толщины тарелки фланца могут быть использованы следующие формулы. Для фланцев с коническим переходом:
если произведение pD =< 1100, то
h_f = s2;
если произведение pD > 1100, то при применении прокладочного уплотнения
;
если произведение pD > 1100, то при применении мембранного уплотнения
.
Примечание. Конструкции фланцевых соединений с h_f < s2 не рекомендуются к применению и не рассматриваются.
Для плоских фланцев, опорного бурта и нажимного кольца следует принять
,
где
= 0,25(p / 10 +1).
8.8.1.1. Расчетные схемы фланцев даны на рис. 8.3-8.6.
Рис. 8.3. Фланец с коническим переходом
Рис. 8.4. Фланец с нажимным кольцом
Рис. 8.5. Фланец с мембранным уплотнением
Рис. 8.6. Плоский фланец
8.8.1.2. Изгибающий момент от усилия обжатия прокладки определяется по формулам:
во фланцах с коническим переходом и в плоских фланцах
Md = Fd l2,
где Fd - усилие, которое принимается согласно п. 8.7.5.1, Н;
l2 = 0,5(Ds - Dm) - плечо действия усилия при затяге, мм;
в нажимном кольце
Md = Fd l4,
Md = Fd l5,
где l5 = 0,5(Df - Dm).
8.8.1.3. Изгибающий момент от усилий, действующих в рабочем состоянии, определяется по формулам:
во фланцах с коническим переходом и в плоских фланцах с прокладочным уплотнением
Mp = F1l1 + F2l2 + F3l3,
где - усилие от действия давления внутри корпуса, Н;
l1 = 0,5[Ds - (D + s1)] - плечо действия усилия F1, мм;
F2 - усилие, которое принимается согласно п.8.7.5.2, Н;
l2 - плечо действия усилия F2, которое принимается согласно п.8.8.1.2, мм;
- усилие от действия давления на внутренний участок тарелки фланца, Н;
во фланцах с мембранным уплотнением
Mp = F1l1 + F4l8,
где - усилие от действия давления на внутренний участок тарелки фланца и мембраны, Н;
Mp = (F1 + F2 + F3)l4;
в опорном кольце
Mp = F1l6 + F2l5 + F3l7,
8.8.1.4. Изгибающие моменты Mh во фланцах, в нажимном кольце и опорном бурте от давления гидравлического испытания p_h, определяются по формулам п.8.8.1.3. При этом в формулах определения усилий F1, F2, F4 вместо расчетного давления p подставляется давление гидравлического испытания p_h, усилие F2 от расчетного давления заменяется на усилие F_2h от давления гидравлического испытания, определяемые согласно п.8.7.5.2.
8.8.2. Определение напряжений по расчетным сечениям8.8.2.1. Моменты сопротивления фланца с коническим переходом определяются по формулам:
для сечения А-А
;
для сечения В-В
, если
=< h_f;
где ;
для сечения С-С
.
Расчет производится, если h_f = s2.
Примечание. Если в рассматриваемом сечении расположен сварной шов, то расчет производится с введением коэффициента прочности сварного шва на изгиб согласно разделу 4.
8.8.2.2. Момент сопротивления плоского* фланца определяется по формуле
.
* Приварка плоского приварного фланца к изделию (труба, сосуд) одним сварным швом не допускается.
8.8.2.3. Момент сопротивления фланца с нажимным кольцом определяется по формулам:
для опорного бурта
;
для нажимного кольца
.
8.8.2.4. Для фланцевых соединений значение редуцированного диаметра отверстия следует принимать:
d_0R = 0,5d_0 при Dy >= 500 мм;
d_0R = d_0(1 - 0,001Dy) при Dy < 500 мм.
8.8.2.5. Напряжение во фланцах во всех сечениях определяется по формуле
o = M / W,
где M- изгибающий момент для трех состояний фланцевого соединения, Н·мм; определяется согласно пп. 8.8.1.2-8.8.1.4;
W - момент сопротивления, мм3; определяется в соответствии с пп. 8.8.2.1-8.8.2.3.
Проверка напряжений производится во всех расчетных сечениях при всех видах нагружения.
8.8.2.6. Для всех сечений и всех видов нагружения должно выполняться условие прочности
o =< [o_f].
Допускается превышение расчетного напряжения в сечениях над допускаемым на 5%.
8.8.2.7. Для оптимизации размеров фланцев рекомендуется:
для фланцевого соединения с коническим переходом
изменить значение s2 в раз, но s2 должно быть не менее чем 1,1 o1, если расчетные напряжения по сечению А-А отличаются от допускаемых более чем на 5%. Расчет фланцевого соединения при новом значении s2 следует повторить начиная с п. 8.7.4.1 до выполнения условия прочности;
изменить значение s2 в раз и повторить расчет начиная с п. 8.7.4.1, если расчетные напряжения по сечению С-С отличаются от допускаемых более чем на 5%;
изменить значение h2 в раз, и расчет при новом значении следует повторить начиная с п.8.8.2.1 до выполнения условия прочности, если расчетные напряжения по сечению В-В отличаются от допускаемых более чем на 5%.
По окончании проверки выполнения условия прочности необходимо проверить условия
Если h2 / (s2 - s1) > 5, то расчет фланца следует повторить начиная с п. 8.7.4.1 при значении s2 = s1 + h2 / 5. Если h2 / (s2 - s1) < 2, то расчет фланца следует повторить начиная с п.8.8.2.1 при значении h2 = 2(s2 - s1);
для плоского фланцевого соединения
увеличить значение h_f в раз, при этом 2h_f должно быть не более чем значение выражения Df - D - 2s1, если расчетные напряжения по сечению А-А превышают допускаемые более чем на 5%. Расчет плоского фланца при новом значении h_f следует повторить начиная с п. 8.8.2.2 до выполнения условия прочности.
Если обеспечить выполнение условия 2hf =< Df - D - 2s1 не удается, то рекомендуется перейти на фланец с коническим переходом.
8.8.3. Проверка толщины тарелки фланцев по предельному состоянию8.8.3.1. Вычисление вспомогательных величин:
для фланцев с прокладочным уплотнением
,
где ;
для фланцев с коническим переходом
при ;
при ,
где ;
для плоских фланцев
;
для опорного бурта
в формулах вычисления вспомогательных величин заменить l1 на l6, l2 на l5:
Если при затяге шпилек используется гидравлическое или другое устройство (без применения крутящего момента), обеспечивающее надежный контроль за усилием затяга, то вместо допускаемого напряжения [o_s] в формулу вычисления коэффициента A подставляется максимальное расчетное напряжение в шпильках, по которому выбран диаметр шпилек;
для фланцев с коническим переходом и мембранным уплотнением
Коэффициенты B, Y, C определяются по формулам для фланцев с коническим переходом и прокладочным уплотнением.
8.8.3.2. Толщина тарелки фланца, определяемая методом предельных нагрузок, равна
Если A =< B, то принимается h_f2 = h_f
Толщина нажимного кольца, определяемая методом предельных нагрузок, равна
8.8.3.3. Во всех случаях окончательная толщина тарелки фланца должна быть не менее толщины тарелки, определенной расчетом по предельному состоянию (см. п. 8.8.3.2).
Для оптимизации размеров фланца производится проверка ранее полученной толщины тарелки фланца сопоставлением значения h_f2 с окончательным значением h_f, рассчитанным в соответствии с п.8.8.2.6:
L = h_f2 / h_f.
При L =< 1,03 для дальнейшего расчета принимается ранее полученное значение толщины тарелки фланца, равное h_f. Если L > 1,03, то расчет следует повторить начиная с п. 8.7.4.1 при значении 1,05s2 для фланцев с коническим переходом и начиная с п. 8.8.2.2 при значении h_f, равном h_f2 для плоских фланцев до тех пор, пока не будет получено L =< 1,03.
8.9. Проверка прочности шпилек на растяжение и изгиб8.9.1. Угол поворота фланца с коническим переходом под действием внутреннего давления и усилия со стороны шпилек
где M - максимальный изгибающий момент (определенный в п. 8.8.) при температуре гидравлического испытания, при 20 °С и рабочей температуре.
Угол поворота плоского фланца определяется по этой же формуле с заменой суммы s1 + s2 на 2s1.
8.9.2. Напряжение в шпильках от изгиба фланца
Окончательные значения d_s и h_f принимаются в соответствии с пп. 8.7.6 и 8.8.3.
8.9.3. Для проверки условия прочности определяется суммарное приведенное напряжение от растяжения (определенное в п. 8.7) и изгиба
o_s = o_0s + 0,6o_sB
которое сопоставляется с допускаемым напряжением
o_s =< 1,3[o_s]
8.10. Выбор размеров и расчет мембраны8.10.1. Исходные данные
Длина (ширина) мембраны принимается равной
b4 = 0,5(D_0m - D) - 10.
Толщина мембраны (s4)j принимается в соответствии с рекомендуемым рядом размеров 4, 5, 6, 7, 8, 10 мм*.
* Значения толщины мембраны s4 приняты по опытным данным ПО "Красный котельщик".
Нерасчетные размеры фланца, обеспечивающие возможность уплотнения мембран (приварка ее к фланцу и сварка мембран между собой), рекомендуется принимать следующими: угол скоса фланца a1 =9°, высота выступа фланца h3 =10 мм.
Мембраны должны изготовляться из листа конструкционной стали марки 20К по ГОСТ 5520. Конструкция мембранного уплотнения представлена на рис. 8.7.
Рис. 8.7
8.10.2. Вычисление вспомогательных величин
8.10.3. Напряжение от внутреннего давления
8.10.4. Напряжение от поворота и раскрытия фланца
8.10.5. Суммарное напряжение в мембране
Задаваясь значениями отношения s4 / b4 от 0,2 до 0,1 с интервалом 0,01 для каждого из значений толщины мембраны (см. п. 8.10.1), следует найти минимальное значение напряжения o_0m, которое и определит оптимальную толщину мембраны s4.
8.10.6. Для углеродистых сталей расчетное число циклов мембраны определяется по формуле
.
Циклом нагружения мембраны следует считать пуск-останов сосуда, гидравлическое испытание и любую разгрузку с последующим нагружением, если при этом величина давления снижается более чем на 30% по сравнению с величиной рабочего давления.
При необходимости выполнения уточненного расчета следует определять напряжения по каждому из указанных трех видов циклов нагружения. Допустимое число циклов каждого вида нагружения может быть установлено по принципу линейного суммирования повреждаемости согласно разделу 5 Норм. Напряжение, приведенное в п. 8.10.3, определяется только по расчетному давлению в рабочих условиях.
Расчетное число циклов соответствует минимальному количеству циклов до разуплотнения мембраны на отдельном участке сварного шва (определенному с запасом 10 по числу циклов) при сохранении плотности на всем остальном периметре шва.
Разуплотнение отдельного участка сварного шва мембраны устраняется сваркой в соответствии с инструкциями предприятия-изготовителя.
Если расчетное число циклов лежит в пределах 100-200, это значение должно быть специально занесено в паспорт сосуда.
Во всех случаях расчетное число циклов должно быть не менее 100. При невозможности обеспечить указанное число циклов должна быть применена другая конструкция мембранного уплотнения.
На сайте «Zakonbase» представлен "НОРМЫ РАСЧЕТА НА ПРОЧНОСТЬ СТАЦИОНАРНЫХ КОТЛОВ И ТРУБОПРОВОДОВ ПАРА И ГОРЯЧЕЙ ВОДЫ. РД 10-249-98" (утв. Постановлением Госгортехнадзора РФ от 25.08.1998 N 50) (раздел 8) (ред. от 13.07.2001) в самой последней редакции. Соблюдать все требования законодательства просто, если ознакомиться с соответствующими разделами, главами и статьями этого документа за 2014 год. Для поиска нужных законодательных актов на интересующую тему стоит воспользоваться удобной навигацией или расширенным поиском.
На сайте «Zakonbase» вы найдете "НОРМЫ РАСЧЕТА НА ПРОЧНОСТЬ СТАЦИОНАРНЫХ КОТЛОВ И ТРУБОПРОВОДОВ ПАРА И ГОРЯЧЕЙ ВОДЫ. РД 10-249-98" (утв. Постановлением Госгортехнадзора РФ от 25.08.1998 N 50) (раздел 8) (ред. от 13.07.2001) в свежей и полной версии, в которой внесены все изменения и поправки. Это гарантирует актуальность и достоверность информации.
При этом скачать "НОРМЫ РАСЧЕТА НА ПРОЧНОСТЬ СТАЦИОНАРНЫХ КОТЛОВ И ТРУБОПРОВОДОВ ПАРА И ГОРЯЧЕЙ ВОДЫ. РД 10-249-98" (утв. Постановлением Госгортехнадзора РФ от 25.08.1998 N 50) (раздел 8) (ред. от 13.07.2001) можно совершенно бесплатно, как полностью, так и отдельными главами.
- Главная
- "НОРМЫ РАСЧЕТА НА ПРОЧНОСТЬ СТАЦИОНАРНЫХ КОТЛОВ И ТРУБОПРОВОДОВ ПАРА И ГОРЯЧЕЙ ВОДЫ. РД 10-249-98" (утв. Постановлением Госгортехнадзора РФ от 25.08.1998 N 50) (раздел 8) (ред. от 13.07.2001)